Kurt Hydraulics in Lyman, NE is set to get a production boost from a new Doosan 2100A 2-axis horizontal turning center and a Techman TM12 collaborative robot. The machining center is designed to machine and sort multiple coupling variations with minimal tending. Kurt Workholding applied the talents of its engineers and robot programmers on this new installation with several more similar units to follow.
Why automation?
With demands on capacity and production speed at an all-time high, it’s been necessary to introduce more automation wherever it makes sense. Kurt’s Workholding division has rapidly increased automation to boost production and to eliminate repetitive lifts and other physically demanding tasks that increase wear and tear on the workforce. Consequently, the employee knowledge base continues to grow with engineers and programmers capable of designing, building and installing complex systems.
Watch the installation testing video below
The Team
Kurt Workholding’s in-house expertise in robotic loading and unloading and round-the-clock operation is contributing to the success of the Kurt Hydraulics division. The multi-disciplinary robotic-automation team for this project included: Connor Rose – lathe-side programming, Matt Ruud – mechanical design for the project, Andrew Porter – electrical engineer for the electronics and communication for the new station and Igor Tretyak – robot programming. This main group was augmented by a handful of others at the Workholding division as needed.
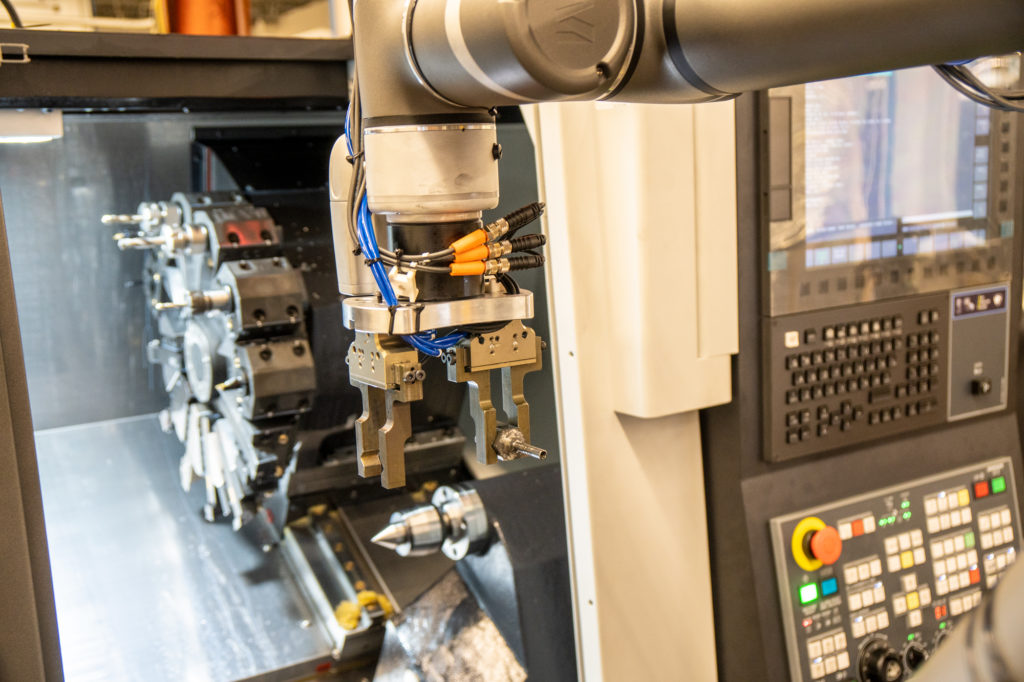
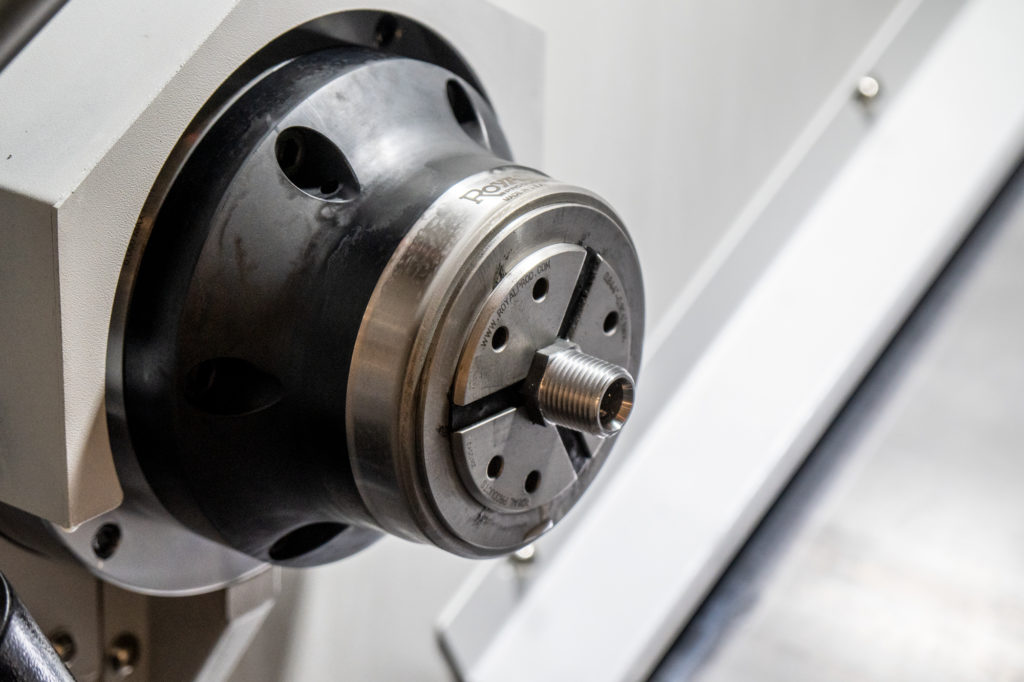
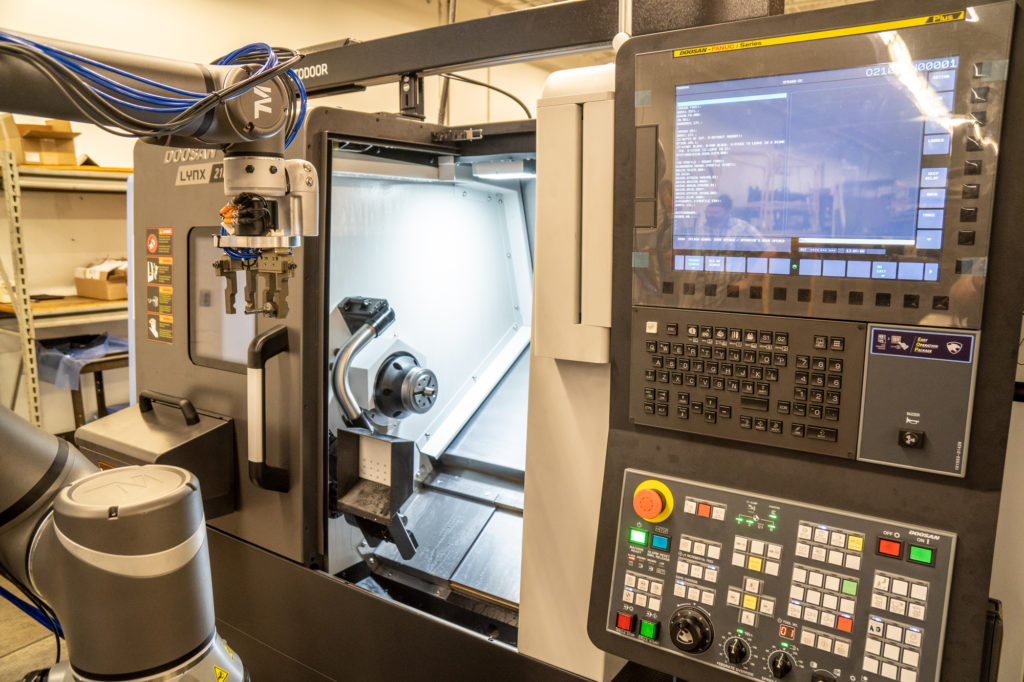
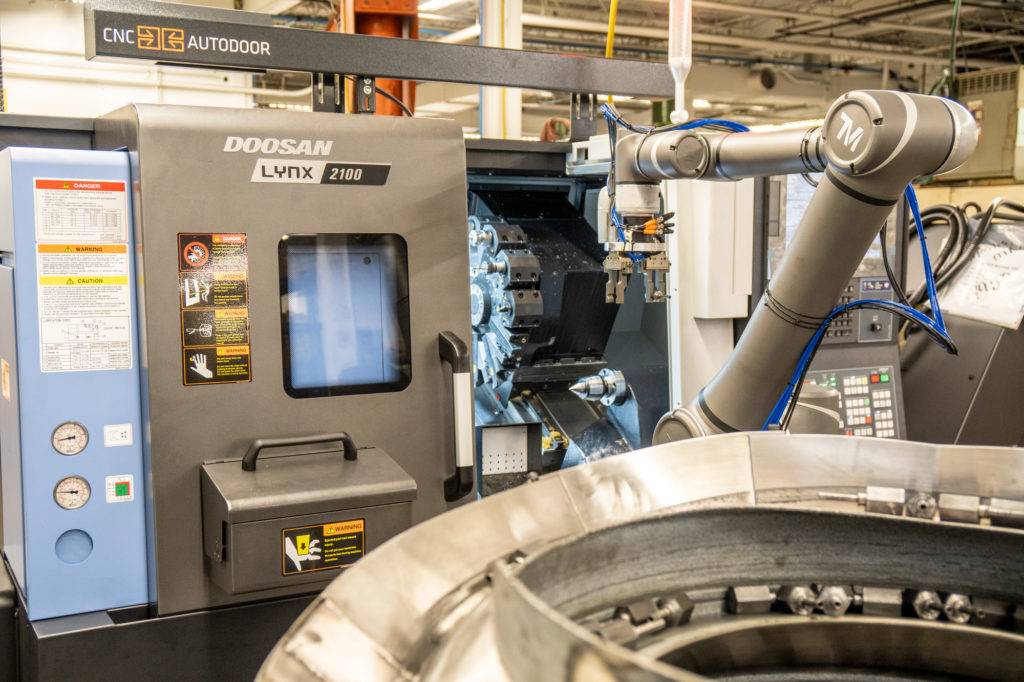
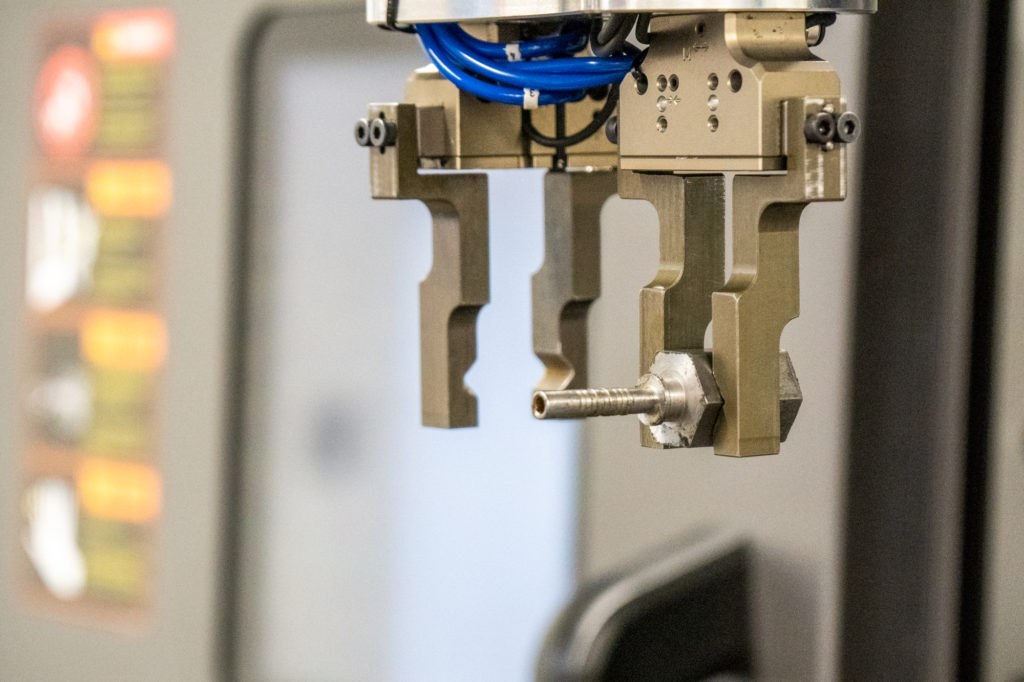
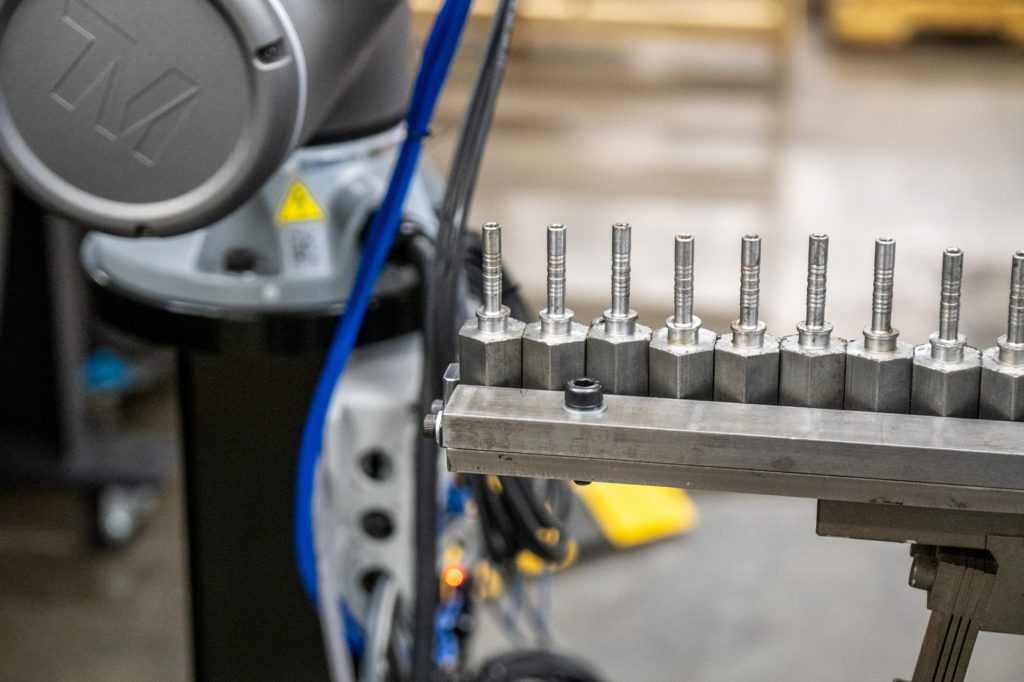
Working with a new machine and robot
Initially, the biggest challenge for the team was working with a new robot and machine they hadn’t interfaced together in the past. “We pretty much learned a new robot from scratch,” said Igor Tretyak. “There were some communications protocols that required a PLC to relay information between the machine and the robot. Andrew Porter was instrumental in figuring all that out. The advantage of getting through this first machine is that several more similar systems are in the works for the Hydraulics division.”
What’s the part and process?
The new machining center will increase production in our Hydraulics facility in Lyman, NE—adding unattended-machine operation and lights-out capabilities to the coupling production line. The new setup performs secondary machining on a coupling blank that’s been turned from hexagonal bar stock with one of our many screw machines. The blanks are sorted in a bowl feeder and lined up and robot fed into the Doosan lathe for a 1-minute operation that cuts threads and bores the coupling. The system is designed to machine up to 30 different coupling variations.
“One of the nice features of this system is that it’s designed to automatically run and sort different part designs,” said Tretyak. “This will allow different quantities of different parts to run without operator input. For example, the system can be programmed to produce 15 of part style A, 50 of B, 72 of C and so on without intervention as one style is complete. The communication between machine and robot will separate each style into a different bin.”
If you’d like to learn more about Kurt’s US-made hydraulic couplings: